|
|
|
|
Framing the interior walls was easier and more comfortable
than the previous work. For one thing, there was now a roof and
windows in place so working on rainy days was not so bad.
I did the interior framing with steel studs. Work moved much
faster than before, and it seemed more rewarding. I still had no
concept of how much work lay ahead. |
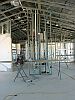 |
|
The dining room coffered ceiling was a bit
tricky. There was some intricate cutting and fitting, and keeping
the whole thing perfectly level required extra diligence. I had a
touch of tendonitis after finishing this job. |
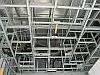 |
|
The electrical branch circuits arrive at
strategic places from beneath the slab. Pulling wiring through steel studs is easier
because the holes are already punched. But a (red) plastic grommet
must be snapped into each to prevent scuffing the wire. |
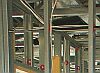 |
|
With steel framing, its a good idea to attach
2X4 wood bucks on the door openings. This keeps it simple for
hanging doors. (Note: This photo was taken with a wide angle
lens, hence the barrel distortion. The walls are not curved.) |
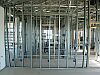 |
|
I was concerned that the cabinet maker may not
know how to deal with steel studs. So I installed steel backing
plates for all the cabinet attachments, and bought a big box of
2-1/2" #8 self-drilling screws to have handy. This way they
can't miss. |
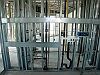 |
|
One issue with steel-framed walls is poor
acoustics. This is remedied by packing the walls with stabilized
cellulose insulation after one side is dry-walled. This was a job
for the professionals. I just took pictures and helped sweep up the
floor.
The same material was sprayed in the attic to a depth of 13 inches
(about R40). |
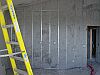
|
|
I'm not built to hang drywall, so I turned the
job over to some guys who had legs growing from their shoulders where
their arms should have been.
This picture, taken November 28, 2000, illustrates something
else. Where the houses in the background are was an avocado orchard
when I started this project and for quite a while after that. |
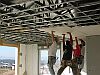 |